Horizontal CNC Milling: When To Choose
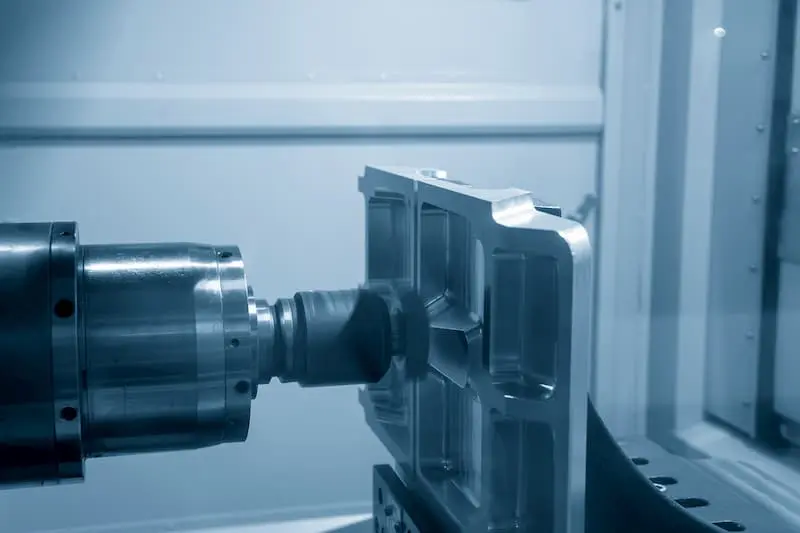
CNC milling is an advanced manufacturing technique for high-precision parts with intricate designs. While vertical milling is commonly used, horizontal CNC milling offers significant advantages in specific applications. This method stands out for its capabilities and benefits. It is often the best choice for complex geometries and large workpieces because of its horizontal spindle orientation and superior chip evacuation.
From landing gear components to armoured vehicle parts, the role horizontal milling plays in machining is endless. This article explains the benefits of horizontal CNC milling and when to choose this method for your machining needs.
What is Horizontal CNC Milling
Horizontal CNC milling is a machining process that functions using a horizontally oriented spindle. You mount the cutting tools on the spindle, which rotates parallel to the work table. This action allows for more efficient and stable cutting. This manufacturing technique differs significantly from vertical CNC milling, in which the spindle is positioned upright. Horizontal CNC milling is highly efficient and precise. They are ideal for machining complex parts with tight tolerance.
Furthermore, some machines use an arbor to hold cutting tools. This allows for greater rigidity and stability when working with hard metals. Horizontal CNC milling has applications when manufacturing parts in modern manufacturing industries like automotive, medical and aerospace.
Advantages of Horizontal CNC Milling
You stand to gain many benefits from using horizontal CNC milling for your project. This machining technique is the preferred choice for high-quality products. Let’s discuss some advantages of horizontal CNC milling.
Increased Accuracy and Precision
With horizontal CNC milling, you can maintain high accuracy and precision throughout the machining process. The machines used are stable, which reduces vibrations when cutting. This rigidity feature leads to tighter tolerances and higher dimensional accuracy. Furthermore, the ability to machine multiple sides in one setup reduces errors caused by manual repositioning.
Enhanced Productivity
Horizontal CNC milling is popular because of its increased efficiency and overall productivity. This process is fast and ideal for high-volume manufacturing. Furthermore, you can use arbor-supported tools that allow multiple cutters to shape a workpiece at a time. This reduces cycle time and gets your product to market quickly.
Improved Surface Finish
The components made using horizontal CNC milling have a high quality and top-notch surface finish. The reasons for this are not far-fetched. You will experience more stable cutting conditions because of the horizontal orientation of the spindle. The tools are rigid and will not deflect in any way. Additionally, the better surface finish can be attributed to efficient coolant application. Coolants flow to the cutting area, reducing heat buildup.
Better Chip Evacuation
Chip evacuation is essential to prevent heat build-up and part defects in CNC machining. Horizontal CNC milling provides better chip evacuation because of the gravity-assisted removal feature. The chips fall naturally from the cutting zone and do not accumulate around the tool. By removing chips as they are produced, you maintain optimal machining temperature and get cleaner cuts.
Reduced Tool Wear
Horizontal CNC milling offers cost-saving benefits in terms of cutting tools. It ensures a longer lifespan for the tools and reduces replacement costs. The tool engages the workpiece simultaneously and distributes the force across. This prevents wear and tool degradation. Because horizontal CNC milling promotes better coolant flow, there is a lower tendency for overheating and tool breakage.
When to Choose Horizontal CNC Milling
Horizontal CNC milling has significant advantages over vertical milling. However, you should not always go for it during part production. The following factors should influence your choice.
Complex Parts with Multiple Features
Horizontal CNC milling is perfect when working on complex parts with multiple features. Multi-axis machining is possible because you can incorporate 4-axis and 5-axis capabilities. Hence, you can use horizontal CNC milling for intricate features like deep cavities and undercuts. Furthermore, with this technique, you can use rotary tables to machine multiple parts in a single setup.
Large and Heavy Workpieces
The horizontal counterpart is better suited for large and bulky workpieces than vertical milling. The spindle orientation allows for more stable support for heavy materials. Additionally, horizontal CNC milling has better fixturing and workholding properties. This reduces unnecessary movement and ensures each part is machined precisely to specifications.
High Volume Production
You should go for horizontal CNC milling when mass-producing parts. With the machine, it is possible to switch between workpieces without stopping. This increases turnaround time in high-production environments. Furthermore, the precision of this technique in high-volume production is second to none. After programming using the right software, the machine produces identical parts with extreme accuracy.
Deep Pocket and Cavity Machining
Not all techniques can machine deep pockets and internal cavities. However, horizontal CNC milling excels in this area for many reasons. The superior chip evacuation makes creating deep pockets easy, as chips do not accumulate. Additionally, the tools you use are shorter and more rigid. They remain stable with minimal deflection when carrying out deep cavity machining.
Specific Material Applications
Some materials, especially hard metals and alloys, are better cut using horizontal milling. Hard materials like steel and titanium should be cut aggressively for better results. Horizontal CNC milling handles this and reduces machining time. Furthermore, this manufacturing method reduces tool wear in tough materials. It provides better cutting angles than vertical mills.
Industry-Specific Applications
Horizontal CNC milling is usually the method of choice for industries that demand quality and precision. For example, the aerospace industry uses high-strength materials, and most parts are made with multi-sided machining. This makes horizontal CNC milling useful for turbine components and aircraft brackets. Additionally, you can use this technique for plastic injection molds and extrusion dies because it meets surface finish requirements.
Conclusion
Horizontal CNC milling offers many benefits, making it ideal in many machining scenarios. It is helpful if you are looking to improve efficiency and productivity when machining complex and high-volume parts. With this manufacturing process, you can optimize production and improve part quality. Do you have further questions and clarifications? Reach out to a reputable CNC machining shop today.